|
Post curing using induction modern induction heating can solve many of these problems.Heating with induction provides reliable, repeatable, non -contact and energy -efficient heat in a minimal amount of time, so that the curing process can be completed with minimal energy and time. |
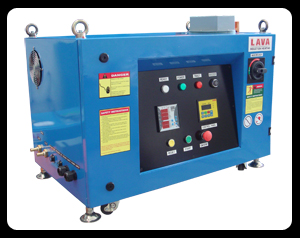
The induction post curing oven 10-20 kVA. system.
|
|
Main specification.
- Power : 380/415V, 3 phase ,50/60 Hz, 10/20 kW.
- Operating frequency : 80-110 kHz.
- Speed : 6 meter oven for up to 25 m/min , 12 meter oven for up to 45 m/min.
- Length : 10 kW 6 meter , 20 kW 12 meter.
- Consumtion typical 6 meter 7-8 KWH, 12 meter 17- 18 KWH.
- Power Unit : 500 (W) x 800 (L) x 500 (H) mm.
- Output Unit : 550 (W) x 900 (L) x 1120 (H).
|
Improved temperature ramping cycles can be achieved with computer control of the solid state power supply.To eliminate extra steps for loading and unloading ovens, induction heat stations can be incorporated into a production line. Finally, induction heating can be performed in extremely clean environments, vacuum conditions or special atmospheres, allowing for unique curing solutions. |
|
|
|
|
Installation with line process. |
|
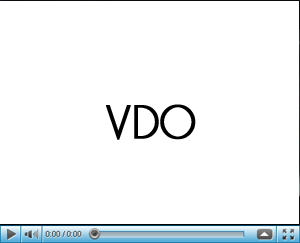
|
|
Main features.
- Close circuit water cool. temperature maintain at 50-70 Celsius to prevent condensation.
- Easy operation ,quick setting.
- No gas piping needed , do not heat up surrounding air, do not produce flame.
- Magnetic field controlled in small circumference , only effective to welding area.
- No heating to bracket , can body or conveyor ,No cooling no conveyor needed.
- Heat produced by the can it self , efficiency of converting heat from electricity up to 90 %
- Energy saving and environmental friendly.
- Simple installation , install directly on top of existing post curing conveyor.
- Temperature controllable, suitable for liquid lacquer and powder repair.
|
|
|
|